How to make the best use of historical data
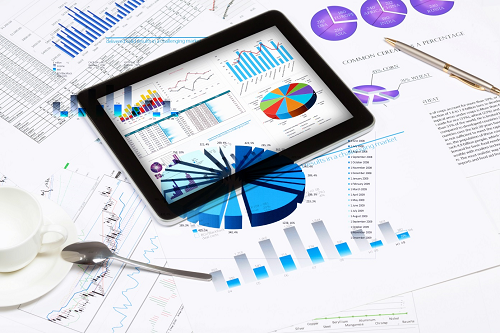
During a project, a large amount of data is collected, assessed and reported by the different parties involved in planning and execution. Think of documentation about design and construction, but also about all other aspects that allow the project to be executed: financial and contractual documentation, planning and risk analysis, quotations, etc. This information is valuable not only during implementation, but also afterwards when the dust has settled.
Each new endeavor leads to new solutions; obstacles are overcome and people learn about many things to further evolve your enterprise. Maybe a risk was mitigated that potentially would have had a big impact. People make mistakes and sometimes take the wrong path. This is only natural, but equally important to capture. Some things you might have no influence on, but it’s good to know about this, so that next time it can be incorporated in the decision making.
Gathering quotations
Quotations and purchase orders form a good example of valuable information to the project team. When part of the design is finished, procurement goes to the market to find suitable suppliers. Estimators can make use of this price information to set up a more accurate estimate. When quotations are carefully stored in the ERP system, including technical data, this information is useful for future projects as well: after thorough analysis often a pattern can be found between specifications and cost of new equipment and materials, making early estimates more accurate. In turn, this can give early feedback to the economic analysis of design alternatives.
Gathering key quantities
During detailed engineering, the design is mature enough for detailed material take-offs to be distributed. It is not before this time that the exact material quantities and construction effort become known. Consequently, this information is not yet available when setting up the budget for this phase. By making clever use of previous projects this information can be used to introduce more granularity to the estimate, even before the (detailed) design is started. This is possible because the industry makes heavy use of design standards. These allow engineers to work efficiently and make that all solutions carry some form of recognition and consistency. After all, it’s not about the scientific ideal solution, but rather the most cost-effective. We as cost engineers can intelligently make use of this as well, by analyzing previous projects, thus distilling typical quantities from the design documents. One example is the typical distance that exists between equipment on the site, which ensures that in advance a good estimation can be made for the length of pipeline between equipment. If the capacity and material type are known, this should give the estimator sufficient information to make a cost estimate that supports a more detailed budget.
Comparing productivity
When setting up the budget and schedule, assumptions need to be made regarding the duration and number of hours needed to perform engineering and construction activities. This is important, because labour often makes up a large part of the incurred costs. When the productivity is higher or lower, a noticeable difference in cost is observed. Determining productivity during project execution is possible by comparing the spent hours with a baseline. This baseline is determined from a standard time norm, found by harvesting data from historical projects.
Location factor study
The same can be done for differences in labour hours between different locations, by making a comparison of hours spent on activities of similar projects, carried out in different geographical locations. This provides valuable information about the difference in cost and productivity which exists between countries or regions to make investment decisions. For example, you might find that a civil excavation in China will most likely be done by hand by a group of people, while in Western Europe this kind of work is typically carried out mechanically. All that knowledge can be used to create location factors.
Close-out report
Of course, all this information has to be recorded first before it can be used for future projects. This is less trivial than it sounds: a project manager will only be too happy to move on to the challenge after his current project is delivered. All parties must consistently capture all relevant data and lessons learned in a close-out report.
Conclusion
The first step for making better use of your historical cost data is to raise cost awareness and get everyone on board. The next challenge is to maintain the discipline that is required to register and index all data. When everything is set up, you can start improving your future budgets.
If you have a question or want to know more about CESK data, please feel free to contact us
.