Cost estimating based on industry standards
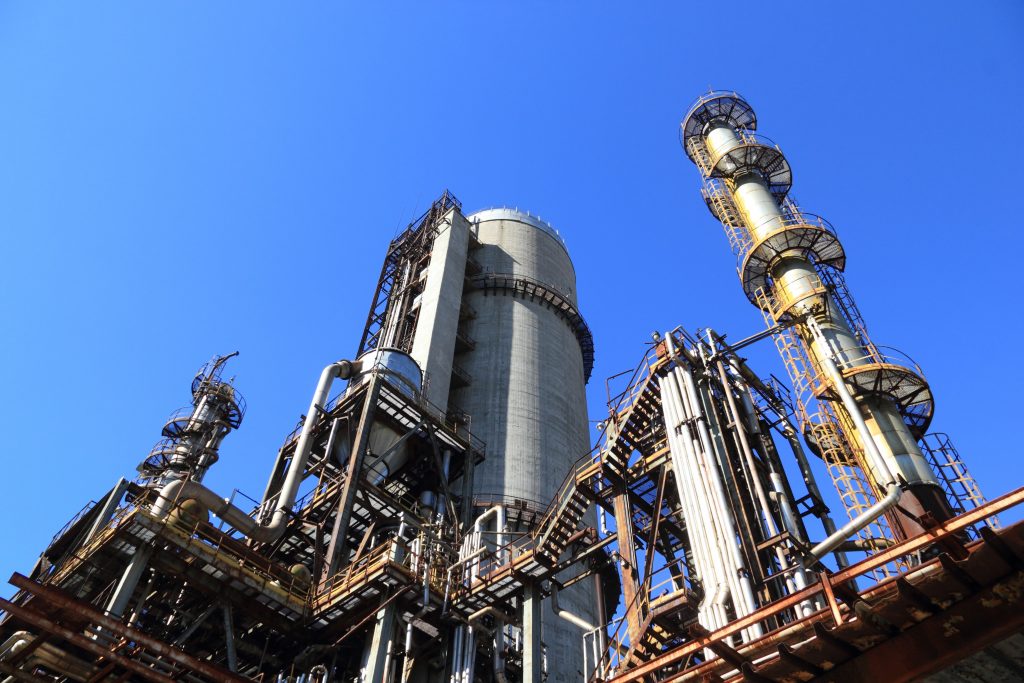
In the traditional sense, an estimate is built-up from the bottom by a large amount of detailed cost data. Although this provides elaborate means of reporting and controlling costs, it is not always possible to make such a detailed estimate given the available time, project definition or type of contract. Therefore many alternative methods have been developed in the past including rough capacity scaling and factor methods. To cover the big gap between these very rough, early estimates and detailed estimates, conceptual quantities can be used. For this we need to develop advanced cost models, possible with state-of-the-art estimating solutions like Cleopatra Enterprise.
This type of cost models are based on industry design standards of processes, equipment and other parts of a project or product that you might possibly want to create. To be able to set these models op properly, a large amount of historical project data is required. The format of this data is just as important: costs should be indexed and normalized.
Depending on the amount of scope information available to the estimator, the models are based on different estimating methods and design standards:
Equipment estimating
The equipment list provides you with technical specifications as input for a cost model about a specific design that you often use. For example, a distillation column often has already defined what its dimension, material type, pressure, and temperature are. These parameters can serve as input for a cost model:
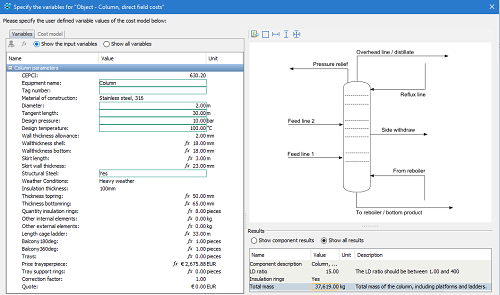
The left side of this example displays the input parameters, of which a number could already be automatically determined from the main specifications, like wall thickness and weight.
Conceptual quantities
Using design standards it is possible to calculate conceptual quantities based on equipment parameters. From the estimated equipment specifications obtained with methods as described above, conceptual quantities are determined for all other disciplines. It concerns only the scope of those disciplines that directly relate to the equipment it is connected to.
For example, the average pipeline diameter and length is based on the type of equipment. For E&I, the number and type of equipment determine the typical quantities of instruments, cables, and number of I/Os. Civil uses the number of equipment to determine the gross floor area and foundation for process buildings.
Initially, the cost model uses automatically calculated properties and values, but when more information comes in, the estimator may adjust the parameters to reflect the current scope. The different sections in the model below (separated by blue bars) provide the estimator with input for the relevant disciplines for a column, like piping, electrical and instrumentation:
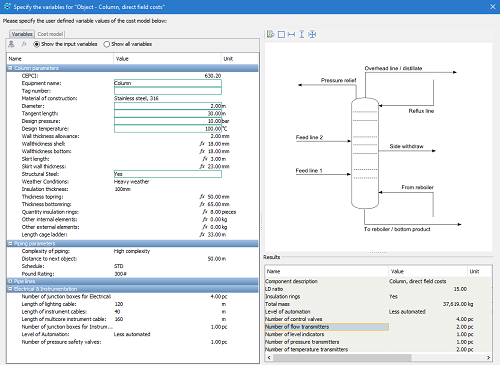
Process steps
The process steps method splits up the plant into functional units, for example, type of process steps, storage facilities, et cetera. Depending on the type of project and industry, many typical process steps could be developed. Per process step all required equipment is automatically included. By varying capacity, the equipment designs are updated and the model updates the parameters accordingly. This provides a very fast estimating method when the equipment list is not available yet.
Below, a part of a standard Process Flow Diagram (PFD) is shown, indicating the different equipment that makes up this particular process (marked in red). Each box represents an equipment model, including related disciplines.

Reference plant
The reference plant method makes use of a standard set of process steps, depending on the type of facility or product. By varying properties of the overall project, the capacity of the various process steps is updated by the model. When it is changed, the equipment models that make up this process should automatically change their design parameters as well. This results in an updated cost. It is basically the same work process as using a rough overall capacity scaling factor. However, where you typically only end up with a single large number, this model now gives you a powerfully amount of details. The interface for the estimator may look quite simple, like below for a chemical plant, but in the background a lot of calculations are being performed automatically.
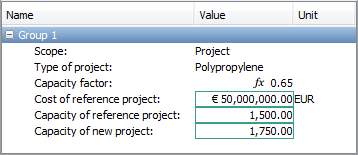
Do you have a question, or do you want to know more about CESK data, please feel free to contact us.