The Role of Cost Modeling in Early Construction Projects
Managing budgets well is very important for project success in the construction industry. Cost modeling helps with this by estimating, allocating, and controlling costs throughout the project in an early stage of project development with limited information.
This blog explains why cost modeling is important, with examples from piping, electrical and instrumentation (E&I), and scaffolding and insulation.
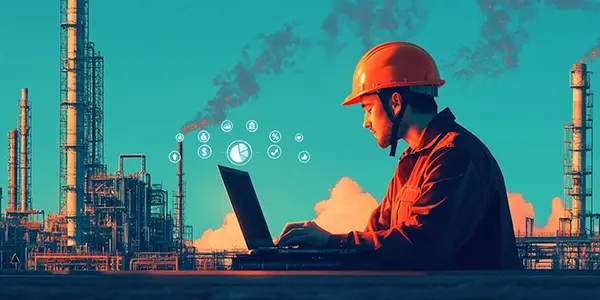
How cost modeling supports early phase cost estimation in construction
Cost modeling creates a picture of the total costs of a construction project while not having detailed engineering input. It helps project managers and stakeholders see where money is spent and find ways to save in an early phase by making correct assumptions about correct disciplines when looking at historical projects. The process includes collecting data, estimating costs, and controlling costs.
Accurate cost models help avoid mistakes in budgeting, standardization estimating ‘’unknowns’’, and support good decision-making. Most often, the disciplines on which no/limited detailed information is available are in an early phase when construction managers just look at the main equipment (pumps, heat exchangers, catalysts, etc.).
Applying cost modeling across construction disciplines
Piping cost models
In large projects in Oil and Gas or Chemicals, piping systems are a large chunk of the overall construction works.
Piping cost models include assumptions about material costs (valves, flanges, fittings, etc.) based on characteristic quantities of required pipe for this project and will aid in labor costs for installation, equipment costs for tools and machines, and indirect costs like transportation and storage.
For example, a cost model for a chemical plant might assume using stainless steel pipes because they are durable and resist corrosion. This very cost model can also come with different assumptions on the number of fittings and valves per meter of pipe. These cost models can also be linked to the main process equipment from which information can be derived to determine, for example, the pipe sizes and material.
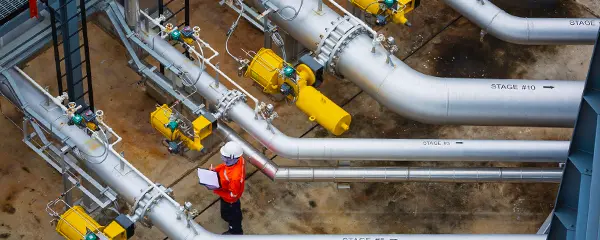
Electrical and Instrumentation (E&I) cost models
Additionally, for Electrical and Instrumentation (E&I), it’s important to have an overview of the total required scope/labor/costs when developing cost estimates for large projects.
E&I cost models include electrical distribution costs like panels and transformers. Including installation and material costs ensures systems work properly.
Another example is the cost model, which would include installing control systems, control valves, cables, and instruments to monitor operations. This is all based on the chosen main process equipment that has been installed.
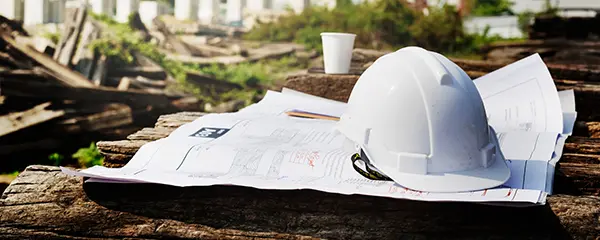
Civil cost models
Also, the main process equipment can be used as an input for the civil cost models for civil foundations. Key parameters include equipment weight, operational dynamics, and footprint and layout.
- Equipment weight: Heavier equipment requires more robust and often more expensive foundations.
- Operational dynamics: Equipment that generates vibrations or dynamic loads may necessitate specialized foundation designs.
- Footprint and layout: The size and shape of the equipment determine the foundation’s dimensions and complexity.
In conclusion, cost modeling is a key tool for forming construction project budgets in an early project development phase. It aids in estimating costs for projects while being able to differentiate the costs in several disciplines. Understanding and using cost models in piping, E&I, and more can lead to significant cost savings in the estimating process and better project management decisions. By using historical data (assumptions vs. actuals), current market trends (pricing and labor norm data), and characteristic quantities, construction managers can draft transparent project budgets ideally used for Final Investment Decisions (FID).