Engineer your cost data by using data software
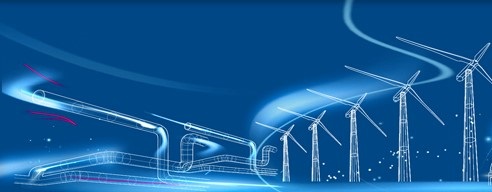
In modern time, processes, design, and construction projects have become smarter and more automated. As much as technology has advanced, estimating techniques evolve as well. Despite the fact that many estimators still use simple spreadsheet tools, the last years brought us advanced estimating software to the market. Instead of using flat data, cost data can be engineered to better and faster determine project costs. How does this work? Let’s look at what is possible these days.
1. Parametric cost models
A modern data software tool allows you to perform regression analysis on data. Make use of this to analyze historical project cost data and quotations to try and find cost estimate relationships (CERs). For example, by studying how the heating area and material type of heat exchangers relate to cost, you might be able to find a formula to predict the cost of future equipment. To do this correctly, you have to index all costs to one price level and make the scope comparable. Performing these kinds of data operations requires an architecture that stores all cost data and cost models in one database that is easily accessible and maintainable.
2. Physical cost models (design standards)
Similar to parametric models, the user can enter design parameters like pressure, temperature, and sizing to obtain equipment costs, labor hours, weight, etc. However, the way the model determines these values is different. Instead of using a formula to directly relate a parameter to cost, an engineering model actually calculates the physical properties of the object you are estimating. It might determine sizes, wall thickness, or installation effort. This allows you to obtain a more accurate prediction and provides more options to tune the model to the specific project scope. This design information is ideally also available to other cost elements in the estimate to calculate costs for other disciplines as well.
3. Assemblies
Assemblies make use of design standards to derive typical quantities for us to use in our estimates. It provides a more detailed estimate that is more accurate and allows us to better control scope growth. The starting point is to analyze a large set of historical MTOs and diagrams to determine the typical build-up of costs. On the smallest scale, this is the combination of a unit of material and all directly related activities and equipment necessary to prefabricate and install it on site. This combination of costs is basically a bill of quantities (BOQ) listing the resources you need to create a single asset or carry out a job. When you start combining these BOQ elements you can build up the costs of a total project. For example, take a length of
When you start combining these BOQ elements you can build up the costs of a total project. For example, take the length of a pipeline. On average, it includes a typical number of pipe fittings, valves, and activities for fabrication and installation per meter. Save this combination in your estimating data software for later use to quickly estimate pipelines. This creates an extra level of detail in your estimates even before you have MTOs to work with.
4. Combining models and assemblies
This is possible when the cost estimating models pass through the (calculated) engineering design parameters to the other components that make up the estimate. It works like this: for each type of equipment, you determine the typical amount of piping, valves, instruments, supports, et cetera. Next time you estimate this equipment, you automatically already have the expected quantities, and thus costs, for all disciplines. This requires minimum effort and yields an enormous amount of detail to work with!
If you have a question, or want to know more about CESK data, please feel free to contact us.